Uma parte expressiva das operações com máquinas móveis, tem a cultura de focar no conserto de máquina parada em detrimento de fazer manutenção. A implantação do PCM – Planejamento e Controle de Manutenção, com cadastros dos equipamentos, seus componentes e suas peças, com atualizados Planos de Manutenção é essencial para sair do Círculo do Desespero.
Um software de manutenção é imprescindível para a geração de ordens de manutenção e acompanhamento de Indicadores de Performance e Custos. O treinamento dos mecânicos para o correto preenchimento das ordens de manutenção é uma tarefa fundamental.
Os indicadores demonstram a vida útil dos principais componentes, tempos gastos nas paradas de manutenção e de operação, pareto de custos com itens utilizados no período, consumo de diesel, de itens de consumo na produção, etc. Um profissional responsável deve estar na retaguarda da manutenção de forma a gerar uma boa estratégia. Mandar nas máquinas e não correr atrás delas.
A maior parte das falhas fornece sinais antecipados de uma eminente parada, como mangueiras com tramas expostas, trincas, desgastes, parafusos frouxos, falta de graxa, sujeira, vibração, ruídos, vazamentos, etc. Esses sinais apontam que será uma questão de tempo o surgimento de uma falha. É o círculo do desespero. Atuar no conserto de uma máquina parada é a pior circunstância do processo.
Máquina parada não produz nada, exceto prejuízo, além de consumir peças e horas de mecânicos, almoxarifes e compradores em desespero. Emergências são onerosas e desgastantes para a equipe. Um bom software de manutenção deve gerar as estatísticas de consumo de peças. A lei de Pareto é altamente aplicável na manutenção de máquinas móveis, em média cerca de 20% das falhas atingem 85% do custo de manutenção.
É muito importante a geração de Paretos de consumo de peças. Uma atenção adicional aos itens classe A, média atenção nos itens classe B e tratamento em massa dos itens classe C. Compra e estocagem de itens classe C devem ser executadas de forma a não gastar mais no processo interno de compra e estocagem do que nas peças. Muitas vezes, um fornecedor único com contrato de valor pré-estabelecido é a melhor opção.
É essencial a estratégia da busca do menor custo entre uma máquina parada versus peça no estoque versus mecânico parado. O custo da máquina parada, sem produzir, é substancialmente maior do que o custo de estocagem e do custo de ociosidade de mecânicos.
Todo o foco do trabalho com máquinas móveis deve ser na produção. O ritmo da produção é determinado pelo ritmo da operação, manutenção e materiais. É mandatório uma cooperação entre estes três setores de forma que um objetivo único seja alcançado: produzir ao menor custo possível e sustentável nos curto e longo prazos.
Em uma visão mais adequada, os três setores são parceiros no negócio da produção e não meros prestadores de serviços. Por sua vez, a produção deve atender os objetivos da empresa. Dentro da visão da ISO 55.000, os setores da empresa devem estar alinhados com um objetivo comum. Infelizmente, ainda vemos departamentos focados apenas nos seus resultados. A visão de cliente-fornecedor para definir a interdependência do sistema produtivo está com os dias contados e gradativamente será substituída por uma estratégia de visão integrada do negócio.
Em nada resolve um estoque excessivamente enxuto de peças de reposição, se o custo de horas paradas aguardando peças ultrapassa o custo de um estoque adequado. Mesmo caso acontece com uma equipe enxuta de mecânicos, se o total de horas aguardando mecânico ultrapassa o custo com salários de mecânicos adicionais.
Para o eficaz gerenciamento desse processo, precisamos de fatos e dados obtidos através de bons indicadores e de uma equipe disciplinada no controle de ordens de manutenção. Um pneu é a única peça de reposição que carregamos em nossos carros, quando em uso normal. A razão é que a falha de um pneu pode resultar em consequências desagradáveis. Eles podem falhar de duas formas: por desgaste natural, fácil de verificar pelo controle visual, ou por um furo imprevisível.
É de fato uma peça de reposição a ser transportada de forma a estar disponível quando necessário. Por que não carregamos, por exemplo, um disco de freio? A razão é que um disco de freio é totalmente monitorável, através de manutenção preditiva, de inspeções periódicas ou por observações do próprio motorista-operador, através de ruídos ou perda de eficiência. Uma falha catastrófica de freios deve ser eliminada por uma adequada manutenção preventiva. Exatamente o mesmo enfoque deve ser utilizado na gestão de peças de reposição. Manter em estoque os itens que possuem falha aleatória e monitorar os itens de desgaste e substituir – quando forem peças de baixo custo ou manter em estoque o mais próximo possível da provável data de fim de vida útil. O planejamento, controle e planos de manutenção, somente são possíveis de serem realizados com a utilização de softwares de manutenção.
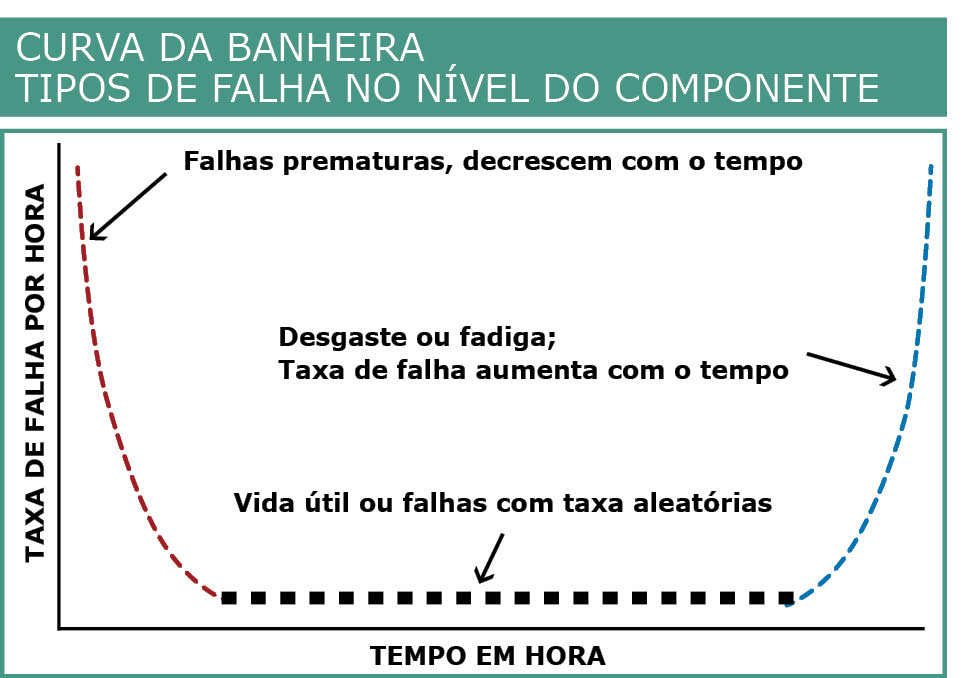
A Curva da banheira, em destaque na ilustração, mostra tipos de falhas no nível do componente. Baseada na área médica, essa curva mostra as três possíveis circunstâncias das falhas e o respectivo consumo de peças de reposição. Para a correta classificação de a qual parte da curva da banheira o item pertence, é imprescindível a obtenção dos dados de vida – tempos entre falhas – dos principais componentes. Com 20% dos eventos, já teremos um controle muito bom de custos, estoques e confiabilidade.
As ocorrências prematuras podem chegar a 30% do total de falhas. São falhas provocadas pelos processos internos da empresa, como falhas nas operações da manutenção, lubrificação malfeita, torques inadequados, serviços improvisados, falta de inspeção, falta de zelo, etc.
As falhas na operação podem ocorrer por operadores mal treinados, utilização além dos limites dos equipamentos, condições desfavoráveis da floresta e falta de zelo. As falhas de materiais ocorrem por uso de fornecedores de peças e serviços de má qualidade, especificações mal elaboradas, problemas com estoques e prazos de reposição. Enquanto estes problemas de processos não forem resolvidos, as manutenções corretivas serão dominantes com elevados estoques das peças afetadas. É mais barato prevenir do que remediar.
As falhas com taxas aleatórias, que afetam principalmente os itens elétricos e eletrônicos, ocorrem por falhas de acidentes operacionais e por desgastes de itens de baixo valor. A utilização de inspeções, baseada em um checklist elaborado pelo PCM é a estratégia de atuação nos itens com essas características, além de estoque o mais próximo possível dos equipamentos.
As falhas por desgaste ou fadiga são as relacionadas ao total de horas operadas pelo componente, principalmente itens mecânicos com peças internas móveis, como bombas hidráulicas, motores, cilindros, transmissão, material rodante, pinos e articulações, buchas, etc. Esses Itens não falham de repente e a manutenção preditiva por monitoramento deve ser aplicada para sinalizar o consumo iminente desses itens para a área de materiais. Não se pode aceitar surpresas com esses itens, pois possuem um alto grau de previsibilidade.