Diferentemente dos equipamentos fixos, devido à interferência de múltiplos operadores com variados estágios de habilidades, as cargas dinâmicas devido aos deslocamentos e às características do terreno, são alguns fatores que tornam a operação com equipamentos móveis mais imprevisíveis e agressivos quando comparado com os fixos.
Mesmo com toda a evolução tecnológica em curso, com unidades autônomas já em operação, os elementos de máquinas continuarão presentes por muito tempo ainda: pinos, buchas, motores, atuadores hidráulicos, mangueiras, engrenagens, somente para citar alguns. Significa dizer que, se não cuidarmos bem, continuaremos a observar folgas, vazamentos, ruídos, aquecimentos, trincas e contaminação. Além disso, as ocorrências reincidentes nos mostram que podemos melhorar algumas partes das máquinas. E já está comprovado que é mais barato executar um reparo de forma planejada do que na forma emergencial.
Sendo assim, a estratégia da manutenção deve ser desenhada para: a) manter ativos em operação, b) melhorar as partes fracas e c) antecipar intervenções, evitando paradas não programadas. Ou ainda, elevar a confiabilidade e melhorar a manutenibilidade. Sair do ciclo do desespero (quebra/conserta) e caminhar para a "classe mundial".
Para atender a estas demandas, uma orientação ideal é a ‘Manutenção 5.0’. Suportada em 5 direcionadores, essa estratégia tem mostrado resultados consistentes e contribuído para que boas empresas atinjam a excelência operacional que tanto necessitam. Os direcionadores são:
1. Atenção aos serviços básicos (manter)
2. O Operador como primeiro cuidador (manter)
3. Eliminação continuada das perdas e desperdícios (melhorar)
4. A manutenção planejada (antecipar)
5. Capacitação constante da equipe
Se você fizer corretamente essas cinco atividades, irá obter melhor desempenho com seus equipamentos.
Serviços básicos: Limpeza, lubrificação, fixação, trincas e folgas. Quatro grupos de serviços que precisam ser executados com rigor e precisão. Se assim não for, geram anomalias que, se não solucionadas no seu estágio inicial, propagam-se e podem causar falhas de grandes proporções. O efeito multiplicador é rápido e destruidor, gerando falhas forçadas continuadamente. É mais fácil, mais rápido e mais barato resolver o problema quando nasce do que esperar as suas consequências amplificadas.
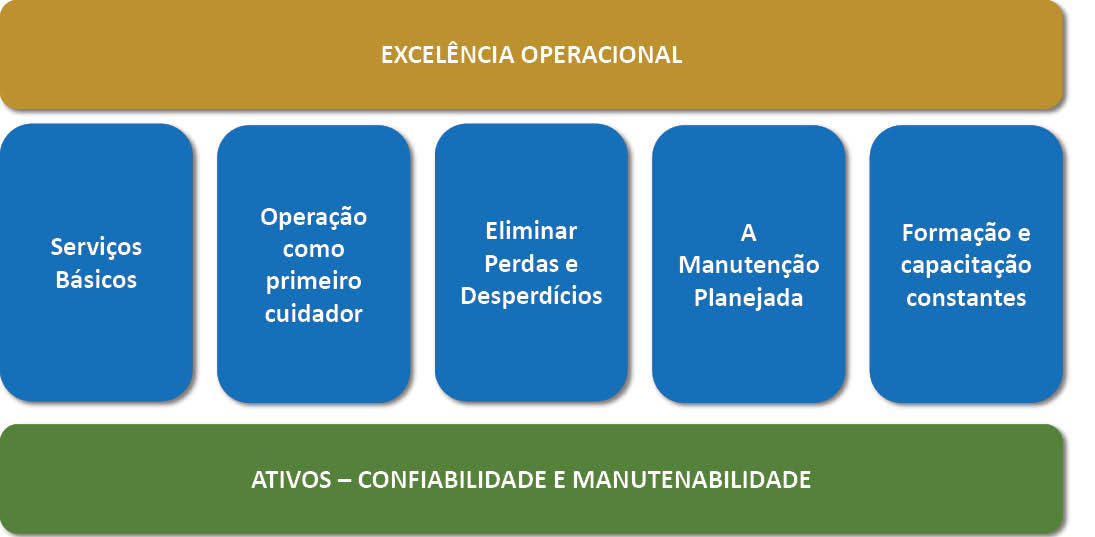
Um conjunto de pino e bucha trocado antes do tempo devido a folgas geradas pela areia colocada juntamente com a graxa, um motor diesel que sofreu superaquecimento devido à falta de aditivo no líquido de arrefecimento, cilindros e válvulas hidráulicas que não atingem a vida útil devido à contaminação do óleo hidráulico e até a perda de uma máquina por incêndio devido a vazamentos e excesso de folhas e galhos, todos esses são apenas alguns exemplos das falhas forçadas geradas pelo não tratamento correto dos serviços básicos.
É preciso conscientizar os operadores e técnicos sobre a importância desses cuidados, pois nem sempre lhes são dados a atenção devida para esses serviços básicos.
A operação como primeiro cuidador: a operação correta é o primeiro passo para a conservação do ativo. O operador precisa atingir os níveis de produtividade cuidando muito bem do seu equipamento. Sempre vale a máxima: "A boa manutenção começa com uma boa operação". O operador conhece bem o seu equipamento e sabe quando a máquina está em pleno desempenho, quando começa a ocorrer perda de função e, finalmente, quando há perda total da função, isto é, quando ocorre a quebra.
A empresa precisa ter um processo estruturado para ouvir o que o operador tem a dizer. E esse mesmo processo precisa ser ágil para dar solução às anomalias que ele relata. Evoluindo um pouco mais, o operador precisa conhecer a relação de causa e efeito entre as inconveniências percebidas para contribuir com o diagnóstico da manutenção.
O gestor operacional tem que entender que, depois do operador, o equipamento é o seu principal recurso. Por isso, é preciso cuidar bem dele. Lembrando que cuidar não é necessariamente consertar, mas estar de prontidão para qualquer anomalia que apareça, encaminhando-a para solução.
Eliminação continuada das perdas e desperdícios: todos os processos possuem perdas e desperdícios, que precisam ser conhecidos em detalhes, para que possam ser eliminados ou reduzidos. Temos perdas no equipamento ou na mão de obra ou perda de material. O sistema de controle precisa ser eficiente para mostrar onde ocorrem e quais os valores dessas perdas. Assim, pode-se criar indicadores para medições e metas a serem alcançadas. A busca para a redução de perdas e desperdícios que, em muitas situações, canaliza os trabalhos para as análises de falhas, é o caminho pavimentado para a melhoria contínua que conduz a um aumento na confiabilidade dos ativos.
A manutenção planejada: para evoluirmos nesse item, o desafio é buscar novas tecnologias e utilizar as já existentes.
A entrada de dados de manutenção é extensa: a) os sensores embarcados que se multiplicam a cada ano; b) as inspeções realizadas pelos mecânicos; c) as solicitações vindas dos operadores; d) a vida útil da máquina que remete a serviços específicos e e) o histórico das ocorrências. O processamento desses dados não é uma tarefa fácil para um analista de manutenção e os sistemas puros de manutenção não estão preparados para efetuar o cruzamento desses dados.
Precisamos evoluir para plataformas integradas de gestão que utilizem algoritmos e outras ferramentas que possam organizar esse imenso banco de dados e, de maneira rápida, indicar as tarefas planejadas para antecipar ocorrências. Nesse novo cenário, as atividades preventivas serão individualizadas. Cada ativo terá sua lista de tarefas prescrita conforme aquilo que as suas informações indicarem. A orientação remota para o trabalho dos técnicos em campo já é uma realidade em várias empresas e deve se expandir nos próximos anos. Assim como o uso de dispositivos que auxiliem no diagnóstico e reparos, com vídeos mostrando exatamente como realizar o serviço.
Capacitação constante da equipe: São as pessoas que fazem as coisas. Elas inventam máquinas, operam equipamentos, realizam manutenção. Não há limite para a capacitação. Já foi dito: "se você acha que a capacitação custa caro, experimente a falta dela". A boa formação e constante capacitação da equipe devem ser priorizadas pelos gestores, utilizando-se de todos os modelos conhecidos: cursos de formação básica, programas avançados dos fabricantes e, principalmente, os treinamentos no local de trabalho. Convém lembrar que a capacitação de um profissional – e isso serve para todas as profissões – depende também dele próprio. Ficar esperando que somente a empresa irá proporcionar essa formação é perder tempo.
A implantação da estratégia com a manutenção 5.0 conduz as operações mecanizadas à excelência, com segurança para os profissionais e custo competitivo. Assim, atuamos no ciclo manter/melhorar/antecipar, saindo do quebra/conserta e avançando para o cenário de classe mundial.