Coordenador de Operações e Gerente de Operações de Transporte da Eldorado, recpectivamente
Construir um projeto de logística florestal apresenta muitos e desafiadores processos, estigmas e padrões preestabelecidos. E, para o caso que relataremos na sequência, não há dúvida sobre as superações necessárias e o empenho do qual lançamos parte. A meta era a de transportar 5,5 milhões de m³ de madeira e construção/manutenção de 1.100 km de estrada por ano para atender a uma fábrica de celulose que iria entrar em operação no final de 2012. Então, como fazer? Qual estratégia adotar? Apresentaremos para vocês nas linhas seguintes.
Primeiro, achamos importante esclarecer que o setor logístico no segmento florestal é historicamente terceirizado, e o início nesse amplo projeto também foi assim, afinal, precisávamos abastecer a fábrica que entrava em operação em forte ritmo. Portanto, nesse início, optamos por seguir a tradição e trouxemos para o startup das operações de transporte de madeira, carregamento e estradas, grandes operadores logísticos, que garantiriam a eficiência operacional e a segurança necessária para aquele período.
Com o passar do tempo, acumulamos alguns experiências ao mesmo tempo em que analisávamos novas possibilidades, que poderiam aliar segurança operacional a custo competitivo. E foi nessa busca pelo melhor modelo logístico e sustentável de conduzir o negócio que iniciamos um processo de primarização das áreas ligadas à logística. Inicialmente, planejamos que, para que essa mudança gradativa ocorresse da melhor forma possível, necessitaríamos de três anos.
Nós buscávamos, naquele momento, resultados que nos garantiriam uma operação inovadora, sustentável e de baixo custo, que nos traria:
• Melhor performance dos ativos decorrente da gestão dos ciclos de transporte;
• Redução do consumo de combustível e consequente redução da emissão de CO2;
• Maior eficiência no carregamento, com consequente melhoria na caixa de carga e no tempo de carregamento;
• Avanços na qualidade em infraestrutura viária;
• Redução de acidentes;
• Sustentabilidade no processo de treinamento e qualificação de MO (mão de obra);
• Garantia de abastecimento fabril;
• Redução do custo logístico da madeira entregue na fábrica.
E, então, a transformação foi iniciada com a primeira aquisição da operação de 92 veículos, 8 gruas de carregamento e a contratação de mais 150 colaboradores na primeira etapa do projeto. Paralelo a isso, havia o desafio de vencer longas distâncias para entregar a madeira na fábrica e a paralisação da hidrovia Tiete-Paraná, que ocorreu logo nos próximos meses após essa aquisição, o que refletiu imediatamente no aumento da frota de transporte em 25%, elevando-a para mais de 400 veículos.
Com o aumento de nosso risco de abastecimento, algumas etapas tiveram que ser aceleradas, como o desenvolvimento e a construção do COE (Centro de Operações Estruturadas) e o início do treinamento da liderança para um novo modelo logístico que estávamos implantando.
Nos dois anos que se seguiram a partir da primeira etapa de aquisição, finalizamos as compras de frotas e nos tornamos, a partir daquele momento, um operador logístico com 300 veículos, sendo 50% próprios, e os demais trabalhando no modelo de agregação, em que o implemento era da companhia.
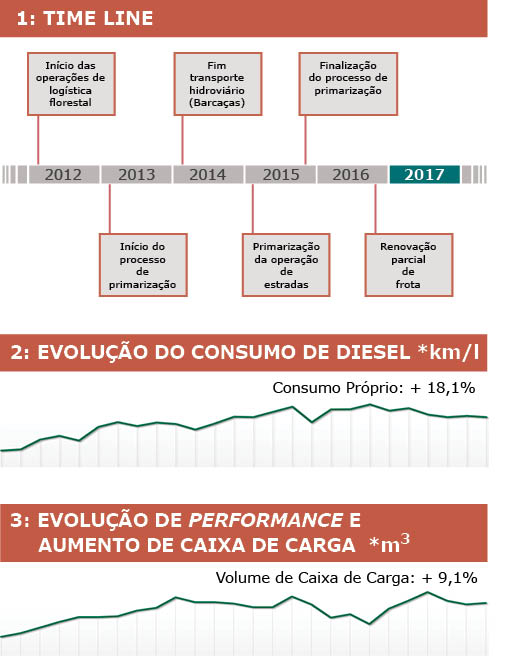
Junto a todo esse movimento, adquirimos também equipamentos para a construção de infraestrutura viária, elevando nossa capacidade construtiva e garantindo a qualidade de nossa rede viária. Ao final do período programado de três anos, podemos afirmar que executamos o projeto em linha com o planejado e operávamos de forma primarizada o transporte, o carregamento e as manutenções e construções de estradas.
Para orquestrar um parque de 300 caminhões tritrem, 35 equipamentos para construção e manutenção de estradas, além dos veículos acessórios, como comboios, pranchas e veículos leves, foi necessário que o COE implantasse o sistema de monitoramento e rastreamento veicular, com o qual conseguimos garantir a assertividade de nossos ciclos produtivos e a comunicação com os nossos colaboradores, em um raio de mais de 300 km utilizando tecnologia por meio de satélites.
Com o advento da tecnologia na operação, com o uso de educador embarcado, um plano de renovação de cavalos mecânicos bem-sucedido, incluindo em nossa frota caminhões sem cubo redutor, em conjunto com treinamento constante das equipes de motoristas, operadores, líderes e supervisores, obtivemos excelentes resultados operacionais, superandos os resultados esperados inicialmente.
• Redução de 7.849 toneladas de CO2 na atmosfera em 18 meses;
• Ganhos de mais de 18% no consumo médio de diesel;
• Aumento de caixa de carga em mais de 9%;
• Ganhos em eficiência da frota em 7%;
• Capacitação e qualificação de nosso quadro de colaboradores.
Ao fim do processo de primarização, entendemos que os resultados financeiros foram conquistados em consequência de uma gestão ativa e de um modelo implantado de forma coerente e planejada. Como se pode perceber, inovar em setores tradicionais exige ampla dedicação, envolvimento das pessoas e, claro, resultados que comprovem que há viabilidade operacional e financeira para a implementação.
Com nosso time, entendemos que, com a constância de propósito e a certeza de que estávamos no caminho certo, seria possível levar adiante nosso plano inicial, que, posteriormente, garantiu o sucesso da operação atual. A solução aplicada à logística florestal na empresa que trabalhamos assegurou o abastecimento fabril com menor custo operacional, maior eficiência e em uma operação segura, sustentável e inovadora.