O setor florestal brasileiro vem se desenvolvendo a cada ano, seja em área plantada ou conservada, com aplicações tecnológicas que têm diversas alavancas de performance na cadeia produtiva, do campo à indústria de base florestal.
No relatório da IBÁ, divulgado em 2021, no Brasil, são plantadas mais de 1 milhão de árvores comerciais todos os dias, atingindo uma área de 9,55 milhões de hectares para fins industriais e outros 6 milhões de áreas de conservação. Esse balanço tem um potencial de estoque de mais de 4,5 milhões de toneladas de CO2.
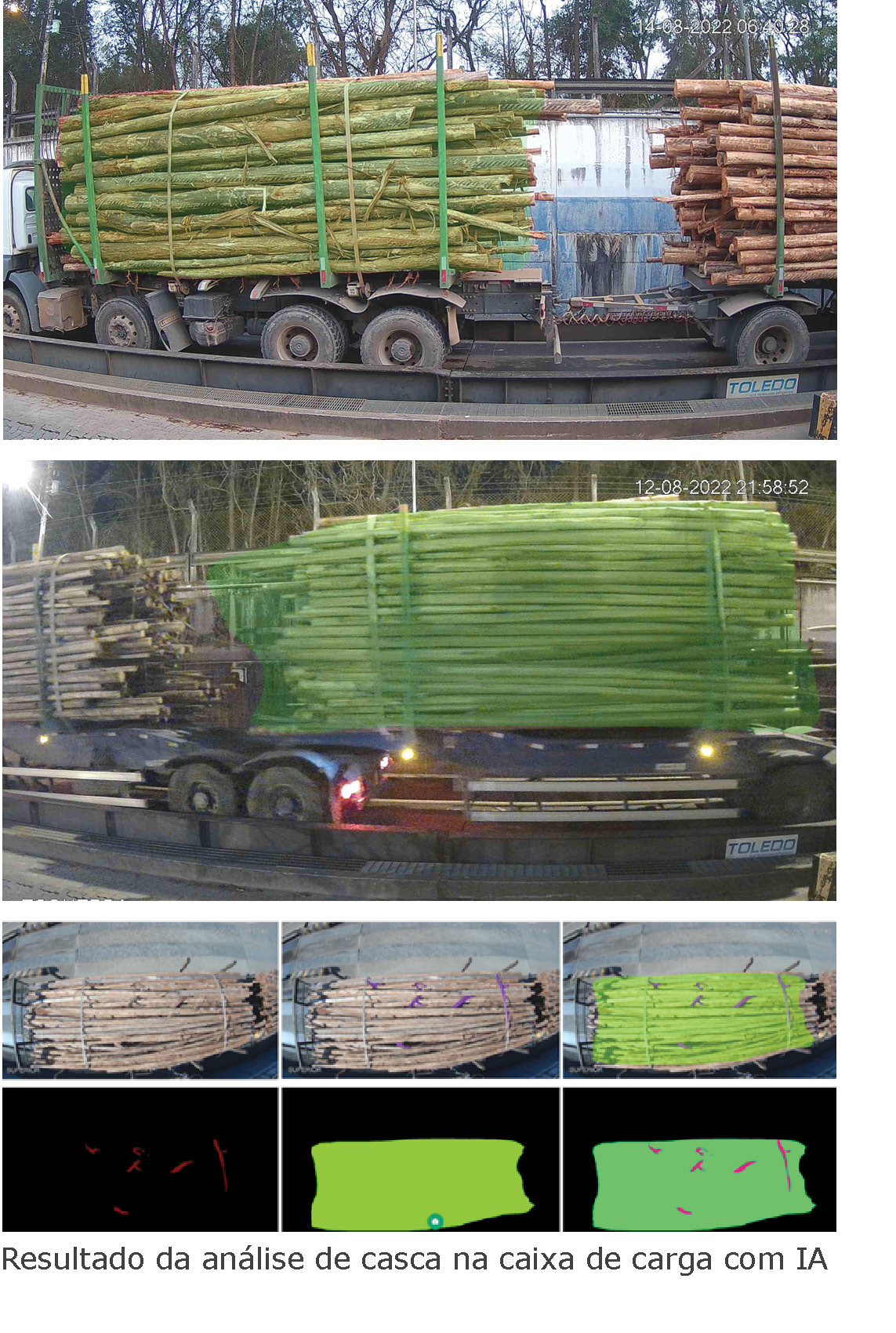
Diante desse crescimento exponencial com a expansão de novas fábricas de celulose e a entrada de novos players no País, vem crescendo muito a demanda por áreas com florestas comerciais para abastecimento e garantia do plano de produção dessas plantas.
Somente no Mato Grosso do Sul, existe a projeção de aumento de produção de celulose de mais de 6 milhões de toneladas/ano. Com esse cenário promissor para toda a cadeia produtiva florestal, por muitas vezes, vem se exigindo das operações de silvicultura, colheita e logística a busca por excelência operacional em suas atividades e processos maximizando a produção e qualidade das madeiras produzidas.
O mercado de celulose mundial está cada vez mais rigoroso com a qualidade dos produtos nas suas mais diversas aplicações, desde embalagens, cosméticos, fibras de tecido com nanocelulose ao tissue. Acompanhando essa exigência do setor, a qualidade da matéria-prima também deve seguir o mesmo critério na floresta, onde os desafios com o impacto da casca da madeira nos processos industriais são enormes.
Eles geram custos altos com manutenção e afetam a disponibilidade de equipamentos no preparo de cavaco e máquinas de papel, consumo de químicos no branqueamento e cozimento até a desclassificação de lotes por sujidade e teor de areia.
Esse equilíbrio entre produção e qualidade passa por alguns pilares que sustentam essa balança e dependem de monitoramento e acompanhamento da qualidade para evitar impactos nos processos de produção das fábricas de celulose. Entre cada processo das atividades da cadeia, podem ser aplicadas ferramentas de avaliações que vão desde uma análise visual das toras com comprimentos-alvo, diâmetros mínimo e máximo, tortuosidade, qualidade no descascamento, danos mecânicos, ataques de pragas, queimadas, entre outros.
Os resultados dessas avaliações são de suma importância para o direcionamento das ações junto aos times de desenvolvimento e colheita, visando a ajustes em equipamentos, capacitação operacional, escolhas de máquinas e cabeçotes mais adaptados para a aplicação, com foco na produção e qualidade.
Como essa etapa de monitoramento emprega equipes que precisam estar se deslocando até as áreas de colheita, que são muito pulverizadas e acabam gerando custos, o setor está passando por uma revolução tecnológica, onde estão sendo desenvolvidas ferramentas de avaliações automatizadas. O uso de inteligência artificial (IA) com objetivo de sistematizar o processo e gerar informações em tempo real com rastreabilidade vem reduzindo esse investimento, aumentando a capacidade de análise em forma de senso dos caminhões recebidos nas fábricas.
Atualmente, está sendo desenvolvido e aplicado o uso de análise de câmeras por meio de modelos que foram desenvolvidos com um banco de imagens onde a IA consegue realizar a identificação na carga de madeira o que é casca e o que é tora. Todo esse processo foi criado no ambiente Digital & Analytics, com a colaboração de startups que apoiaram no desenvolvimento do modelo construído a partir de mais de 2.000 imagens em uma rede “colab”. Assim, foi possível gerar uma melhor assertividade do software com a calibração das medições manuais, visando a uma correlação alta do resultado da análise da Inteligência Artificial na mensuração do índice de casca na carga.
Essa informação pode ser gerenciada pelo time de logística inbound para o direcionamento e tratativa dessa carga no primeiro momento, evitando que as cargas com alto índice de casca sejam consumidas. Estruturalmente, é gerada a informação de qual local essa madeira foi transportada e, consequentemente, colhida, dando rastreabilidade ao time de desenvolvimento e excelência operacional para que realizem as devidas ações de correção.
Com a aplicação dessa ferramenta via POC (prova de conceito), foi possível observar a redução no teor de casca do cavaco que alimenta o digestor, garantindo um gerenciamento da qualidade da madeira nos processos industriais, reduzindo os custos e evoluindo nos elos da cadeia produtiva florestal.